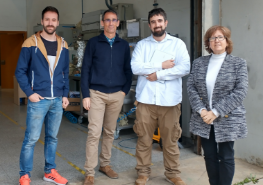
05 May 2022 / News
The importance of simulations in research projects
Reactor simulation – Unit scale models
The reactors used in AlSiCal project involve complex multiphase systems and coupled dynamic phenomena. Our modelling approach successfully addresses the thermodynamic description of the systems and the process kinetics. For that purpose, we implement classical chemical engineering models in a suitable thermodynamic simulation environment.
The models first serve as a decision-making tool to delineate the operating windows allowing to get the desired products. For instance, regarding anorthosite dissolution (WP1), the thermodynamic modelling developed in WP1 allowed to find HCl and solid concentration ranges that allow selective precipitation of amorphous silica, with other constituting elements leached in the aqueous solution.
Then the thermo-kinetic model helps to distinguish the separate effect of each elementary process and its impact on the reactor performance, which is difficult to achieve through experimental measurements. Nonetheless, experimental data is needed to check model predictions and/or calibrate sensitive model parameters (rate law parameters, mass transfer coefficients).
Once the reactor model is validated, it can be further used to optimize the key operating conditions according to a precise objective, as well as to investigate process scale-up – such as the effect of switching from batch to continuous processing, and to propose suitable configurations (sequence of operations, reactor configurations).
The models help to identify the rate-limiting process(es) among all the implied phenomena, which is useful to propose new technologies that can alleviate this(ese) highlighted bottleneck(s).
LGC- Toulouse
Process simulation – Large scale models
For AlSiCaL project, UNIZAR is responsible of supporting in the assessment the technical, environmental, economic and socio-economic performance of the AlSiCal alumina process. This includes finding the optimal process conditions for the new technology compared with currently applied alumina production.
Within AlSiCal we do this by developing a complete process simulation to quantify the energy and material requirements of a base-case process, the operation of each individual sub-system and its thermochemical behaviour in order to verify and quantify the different possibilities for reducing energy consumption.
The optimization process involves the development of a global (energy and material) computational model to simulate in detail the integration of different energy and material streams. The objective of this task is to find synergies between subprocesses in order to minimize the energy and material requirements, pollutant emission and waste generation. The tasks will also define the rough values of key operating parameters, such as the energy requirements in leaching and calcination processes, heat loads of the heat exchangers, and the power loads of different equipment
The AlSiCal process includes the integration of a CO2 capture system to minimize also the CO2 emissions of the process and valorise them. The objective of UNIZAR together with other project partners is to propose a layout and quantify the energy and material streams (input and output-waste) for a process without CO2 emissions. Due to the necessity of a calcination process and the presence of Calcium, the most suitable process for CO2 capture is the Calcium-looping process. Synergies can be found between Carbon capture and the AlSiCal process that lead to a reduction of the impact of the CO2 capture into the overall alumina production process.
Finally, UNIZAR also support in the calculation of the proposed process production costs to select and justify investment decisions (techno-economic feasibility) in an industrial scale future scenario that are also environmentally sound. Despite being at low/medium TRL level, together with coordinator and industrial partners, we try to size and estimate cost for industrial scale, bringing the exercise closer to reality.
Evidently, to obtain detailed and realistic results, all of these tasks need input from other project partners. Their support, knowledge and experimental data are essential for our work, and our conclusion are also relevant for further studies within the project.
The AlSiCal project and how both scales come together
Modelling the phenomena behind the performance of the individual reactors involved, as well as their integration within the AlSiCal overall process can help to find optimization avenues to improve its environmental footprint and to reduce its costs.
The Innovative Multiphase Reactor Engineering (IRPI) Reaction engineering, multiphase (catalytic) reactors group develops innovative or breakthrough processes for multiphase media. The fields of application of its research concern in particular chemistry, energy, new materials, the environment and depollution, and new technologies. They are part of the Chemical Engineering Laboratory (LGC) from the University of Toulouse.
The UNIZAR team is composed by a multidisciplinary team of chemical, mining and mechanical engineers with wide expertise in process simulation, energy analysis, CO2 capture and the assessment of social implication of energy issues.
Our role in AlSiCal is basically what we do within “Energy and CO2” research group at UNIZAR, trying to close the gap between Academia´s basic knowledge and real industrial processes in issues related with energy and CO2 emissions.
Are you interested in the work performed by LGC and UNIZAR? Please don’t hesitate to contact us to find out.