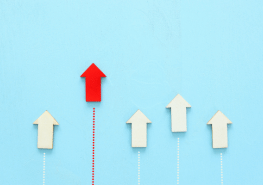
15 Dec 2023 / News
Life Cycle Assessment (LCA): Advantages of the AlSiCal technology
During the AlSiCal project, detailed Life Cycle Assessment (LCA) has been performed by AdMiRIS, in collaboration with UNIZAR and IFE. Several cases have been evaluated in this study:
i) Different AlSiCal process configurations assuming renewable energy input; ii) the same AlSiCal processes, but assuming fossil fuels input; and iii) the current industrial technologies (the State-of-the-Art (SotA)), as it is described in the Best Available Techniques (BAT) documents and LCA-related datasets, to produce the same products as the AlSiCal technology case.
The AlSiCal “anorthosite-to-alumina” system
The AlSiCal “anorthosite-to-alumina” system includes all the material and energy inputs for the holistic processing of anorthosite into alumina and the other co-products. The Life Cycle Inventory was provided by UNIZAR and IFE, taking into account upscaling and optimization aspects for the entire flowsheet of the potential AlSiCal plant. The process ensures high-resource efficiency, while the contemplated metallurgical plant has (1) proximity to anorthosite mine, (2) zero direct carbon dioxide emissions, (3) access to renewable energy and renewable hydrogen, (4) no bauxite residue production and (5) coproduction of three products. The environmental performance of the AlSiCal technology was compared to the environmental performance of SotA.
The results
The results clearly show the large environmental benefits of AlSiCal technology compared to SotA, among them:
- The energy consumption for the simultaneous production of alumina, precipitated calcium carbonate and silica -to be used as precipitated silica substitute- with the AlSiCal technology is significantly lower than the total energy consumed to produce these materials with the SotA technologies, based on data found in LCA-related datasets and the Best Available Techniques (BAT) documents.
- The impact categories related to emissions to air, such as Climate change, for producing alumina, precipitated calcium carbonate and precipitated silica with AlSiCal technologies are significantly lower compared to the current BATs producing these materials.
- The electrification of the AlSiCal processes results in the minimization of the impact related to emissions to air.
- The lower energy requirements, the easy access to green-energy mix and the much shorter distance of anorthosite mine to the plant, comparing to the average distance for bauxite transportation to Europe, make the AlSiCal technologies more environmentally friendly.
- One of the principal advantages of AlSiCal is that it does not generate waste, and particularly, bauxite residue. Of major importance is the avoidance of large volumes of bauxite residue (0.8 t/t alumina) and the impact of bauxite residue landfilling to categories related to the eutrophication and the toxicity for humans and environment.
Important milestone
The completion of LCA for AlSiCal technology with such positive results is an important milestone. It confirms and quantifies the desired positive effects of this technology for coproducing alumina, silica and calcium carbonate. Based on the current findings, processing anorthosite by AlSiCal is clearly a more sustainable technology than SotA to produce critical and essential materials for our future.