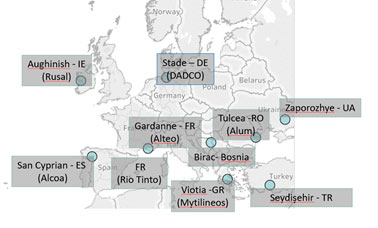
15 Dec 2020 / News
The industrial alumina production processes in Europe and their environmental aspects
Within the AlSiCal project you hear a lot about environmentally friendly ways to produce alumina from alternative production route than from bauxite. Our project is committed to research new sustainable ways to de-risk the alumina production process. But which are the current industrial alumina production processes in Europe? This article shortly describes the main aspects of the Bayer process, the primary process by which alumina is extracted from bauxite.
Aluminium
Aluminium is an abundant metal in high demand, due to its desired properties and application possibilities for everyday usage. Predictions by AlSical partner European Aluminium state that by 2050 global demand for primary aluminium is expected to increase by 50% reaching about 110 million tonnes. Today, aluminium is mostly produced from bauxite, arising from different sources. Processing this mineral, via the so-called Bayer process, results in alumina (typical name for aluminium oxide), that is being used in the current industrial processing route for the production of aluminium.
Alumina production: Bayer process: & calcination
Alumina is produced from bauxite in the well-established Bayer process, followed by a calcination process. This Bayer process was invented in 1888 by Carl Josef Bayer and contributed with the development of aluminium to the ongoing industrial revolution. The Bayer process produces pure aluminium hydroxide from bauxite. As shown in the figure below, this process utilises the different thermodynamic properties of the caustic soda – aluminium hydroxide system and typically consists of the following stages: bauxite crushing & grinding, leaching, physical separation, precipitation and crystallization of Aluminium hydroxide which is filtered and recovered as a cake. After drying, this cake is calcined, usually in a fluidized bed furnace, to produce chemical grade or metallurgical alumina.
Fig. 1 : Main alumina refinery processes: Bayer process and calcination (Image courtesy of Mytilineos SA)
The Bayer process typically consists of the following stages:
- Preparation of bauxite (bauxite crushing & grinding)
- Digestion under pressure (leaching)
- Solid-liquid separation
- Precipitation and crystallisation of aluminium hydroxide
- Filtration & drying of the precipitate
The last step of the Bayer process is calcination. Through this process, the hydrate, i.e. Al(OH)3, is converted into alumina, i.e. Al2O3. This calcination takes place nowadays mostly in fluidised bed calciners at temperatures around 1200–1300°C.
The mainly used Bayer process involves many separation and preparation steps which require either a high amount of chemicals or energy. Since some essential chemicals, e.g. NaOH, are cost intensive for the process within the extraction process, producers aim to recover as much as possible those chemicals for reuse within the Bayer process. Companies are for example highly interested in decreasing soda/aluminate solution losses, and are therefore searching for ‘dewatering’ the bauxite residue slurry. As example, filter press technologies are used to separate and to rinse bauxite residue from the liquor. Nevertheless, those technologies are expensive considering the huge volumes of bauxite residues (700-800kg/tonne of alumina). Therefore, there is a high desire for both an easily manageable by-product as well as the need to minimize waste streams. Hence, the industry is highly motivated to develop technologies for waste recovery and circular production processes.
In this respect, the AlSiCal project can offer an alternative production route based on the utilization of largely available ores which can be sourced in Europe.
Environmental impacts of alumina
Today, bauxite is mostly mined in tropical areas like Guinea, Brazil or Australia. Hence, the majority of the bauxite used in Europe is imported, i.e. about 14-15 Mt/year, with the exception of Greece which produces 2 Mt/year used locally. Mining bauxite leads to an impact to land and in usage of raw materials, energy, air emissions and tailings. However, these impacts are relatively limited compared to impacts appearing downstream in the value chain, e.g. alumina plant .
About 7 Mt/year of alumina is produced in Europe, i.e. 7% of the global production which reaches 130 Mt/year. This generates about 5-6 Mt/year of bauxite residue in Europe. The Alumina plants located in Europe are reported in Fig. 2.
Fig. 2 Alumina plants located in Europe
Hence, many initiatives focus on reducing the environmental footprint of the Bayer process by turning bauxite residue into resources, in order to produce alumina as sustainable as possible. The on-going EU Horizon 2020 Removal project for example aims at developing sustainable processing routes for various bauxite residues flows generated in Europe (see www.removal-project.com ).
The AlSiCal Project – a possible alternative for the Bayer process
The AlSiCal project tries to offer an alternative for the current Bayer process, in order to realize a sustainable alumina production by further researching, developing and de-risking the ground-breaking AlSiCal technology. By integrating CO2 capture, this technology enables the co-production of alumina, silica and precipitated calcium carbonate, using new resources – e.g. anorthosite, abundantly available worldwide – whilst generating ZERO Bauxite residue and ZERO carbon dioxide (CO2) from production. This alternative will both position Europe at the forefront of innovation for the Green Shift for the mineral and metal industry and unlock substantial reserves of new resources within the European Union – and from worldwide available resources – that can complement or substitute today’s worldwide production of alumina under sustainable principles.